Fabric formwork physical modelling: different fabric tests
- Oliver Haigh
- Mar 16, 2020
- 2 min read
Updated: Nov 23, 2020
For the next phase of physical testing, I wanted to look at how different types of fabrics or membranes would affect the casting process and the final form. I decided that I would revert to the loose-hanging method for this, as this gives the fabric the most freedom to respond to the plaster in accordance with its own material properties, unaffected by me imposing tension or particular forms upon it. The second elastane test that I did is added into this to complete a batch of four casts using four different materials. The other materials are calico, a needle-punched geotextile, and polyproprylene.
Film documenting various aspects of the different fabric comparison tests
I have found film a particularly good medium for documenting and representing these tests (see above), as it conveys the tactility of the fabric removal process, and shows texture and form well together as well. I also used film to document the evidence of the permeability of some of the fabrics – water dripping through during the process.
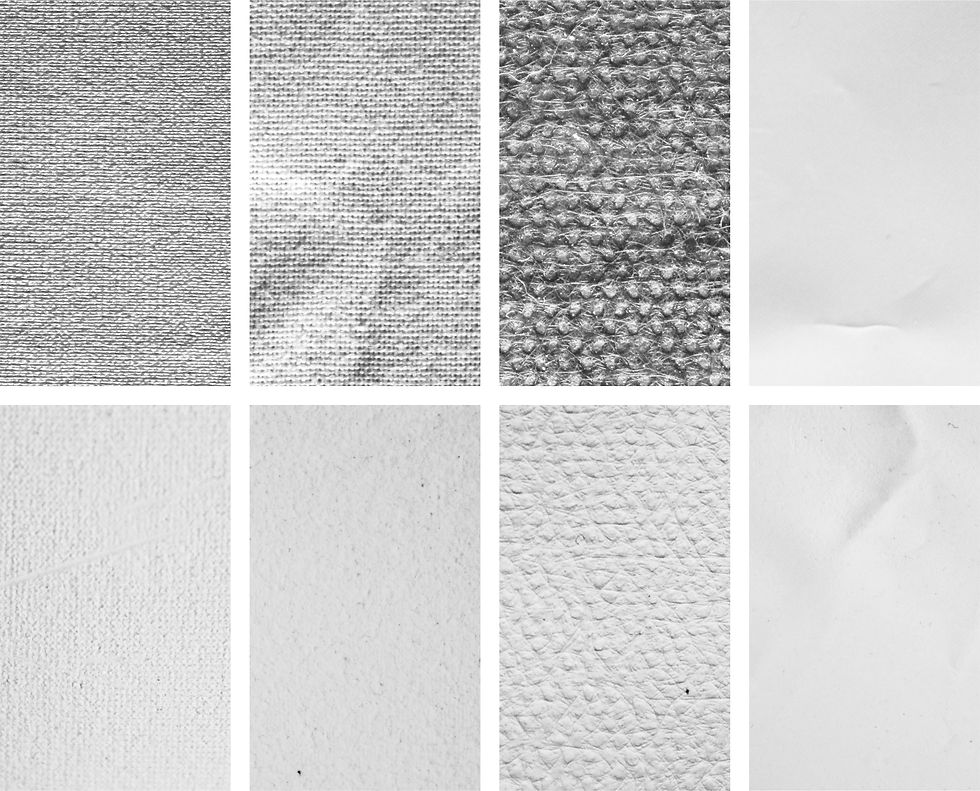
Textures of each fabric (top) and its respective cast surface (bottom); (left to right) elastane, calico, geotextile, polypropylene
The photos above show how changing the fabric used changes the texture of the resulting cast surface. The cast material will pick up any of the detail and texture of the fabric being used, which is why the geotextile cast has the most pronounced pattern, whilst the polypropylene cast is smooth.
The photos below show each iteration as it is was being cast, as a plan view of the who final cast, and then a close-up photograph conveying the types of form being created.

Elastane

Calico

Geotextile
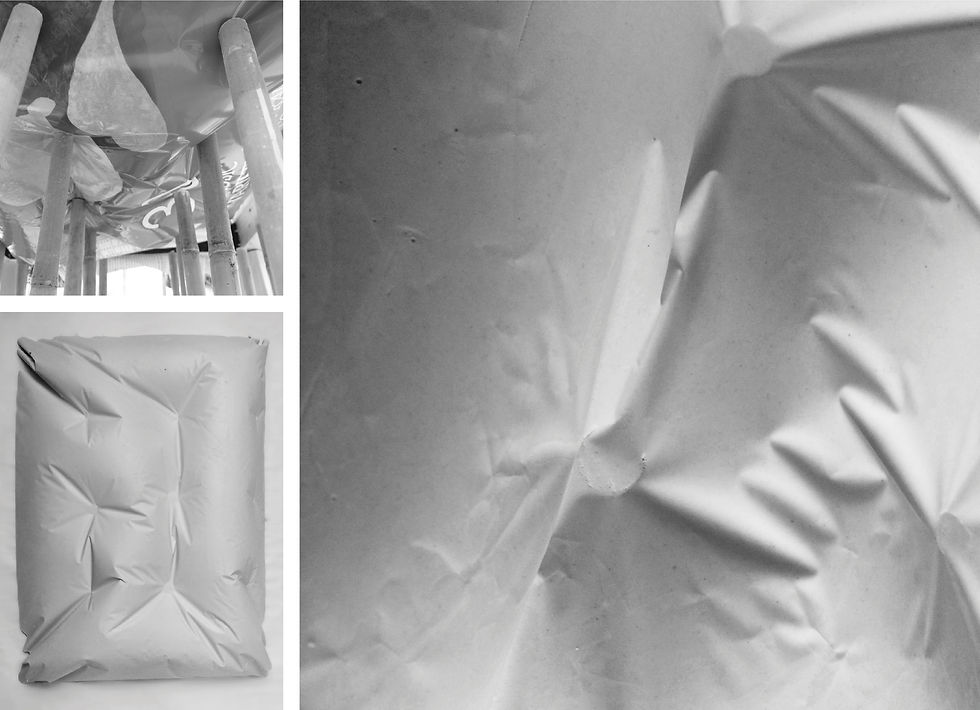
Polypropylene
There are a few interesting points of variation between the four different tests.
It is clear to see that formally, the elastane leads to the most undulating forms, as the fabric deflects to a much greater degree under the weight of the plaster than all the others, due to it being a very elastic material. All the others are fairly inelastic. The result of this is that all other tests display creasing on the surface, to some greater or lesser degree, which I find to be quite an aesthetically pleasing effect.
Looking back at the process photos, it can be seen most notably with the geotextile and calico that excess water from the plaster mix seeped through the fabric. This also happened with the elastane. The polypropylene was the only one which didn't allow any water to leave during the process. The result of this is that it took much longer to dry than the others, and also that the surface appeared weaker, with bits chipping off the edges much more easily. This is because the surface is not as plaster rich. This is a phenomenon that Mark West talks about with concrete casting in fabric formwork, citing it as one of the benefits of the fabric formwork process.
Comments